Evaluating Various Techniques for Optical Fiber Connector End Face Processing
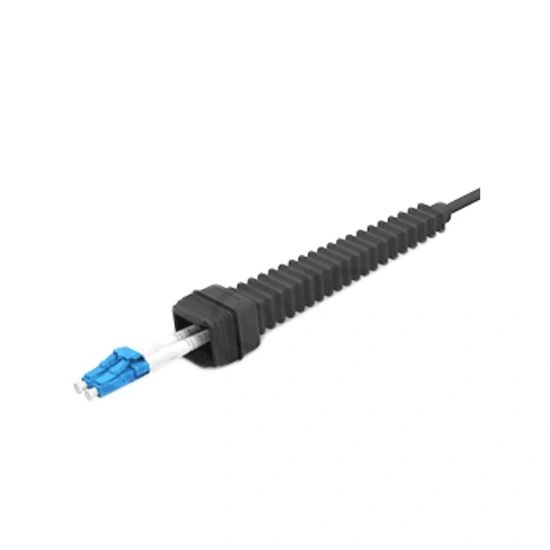
Optical fiber connectors play a pivotal role in transmitting high-speed data across networks. The performance and reliability of fiber optic systems greatly depend on the quality of these connectors. A key factor in ensuring optimal connectivity is the end face processing method employed. This article comprehensively explores different types of end face processing methods for optical fiber connectors and compares their impact on overall performance.
1. Mechanical Polishing
Mechanical polishing is a widely-used method for end face processing due to its simplicity and effectiveness. It involves using abrasive materials to gradually remove any imperfections or irregularities on the connector's end face. This process provides a smooth and flat surface, facilitating efficient light transmission. However, it requires skilled technicians to achieve precise control over the geometry and finish quality of the end face. Additionally, the process is time-consuming and can lead to thermal damage if excessive pressure or friction is applied.
2. Chemical Etching
Chemical etching is an alternative approach to polishing that employs a chemical solution to remove impurities and improve the end face quality. This method is especially suitable for connectors with angled polished connectors (APC) as it can create highly precise surface profiles. The etching process, however, requires strict temperature and duration control to prevent over- or under-etching. It also entails the use of hazardous chemicals, necessitating appropriate safety measures during the processing.
3. Plasma Treatment
Plasma treatment involves exposing the end face of an optical connector to a low-pressure plasma gas. This process modifies the surface properties by eliminating contaminants and creating a clean interface for superior optical performance. Plasma treatment offers several advantages, including flexibility in adjusting surface energy, reduced risk of damage to the connector, and compatibility with various connector geometries. However, the equipment for plasma treatment can be expensive, and the process requires strict control to ensure consistent results.
It is essential to consider the intended application and specific requirements while selecting an end face processing method for optical fiber connectors. Each technique has its advantages and limitations that need to be weighed against the desired outcome.
Comparative Study of Impact on Optical Fiber Connector Performance
All end face processing methods impact the optical fiber connector's performance, including insertion loss, reflection, and durability. Mechanical polishing generally achieves low insertion loss and reflection, but long-term stability may vary due to the vulnerability of the polished surface. Chemical etching, on the other hand, offers enhanced stability and minimal insertion loss for APC connectors. However, the reflection sensitivity to environmental factors presents a challenge. Plasma treatment provides excellent insertion loss and reflection performance, with high stability and environmental resistance. Nevertheless, the initial investment and complexity of the process should be considered.
Conclusion
Choosing an appropriate end face processing method for optical fiber connectors is crucial for achieving reliable and efficient network performance. Mechanical polishing offers simplicity, while chemical etching enables precise APC connectors. Plasma treatment combines excellent performance with durability. Understanding the characteristics and trade-offs of each method assists in making informed decisions for optimal end face processing.